Scattered Parquet Production Process
14 basic steps of manufacturing scattered parquet
Meeting for Preparation
Scatterered Parquet products are very beautiful product, but need accurate calculation and planning.
Before we start manufacture, we’ll arrange a serious meeting with production manager and products designers to discuss the details of each certain pattern, like percentage of each shape required, Tongue and Groove direction, most stable structure, Coating plan,Packing plan.etc..
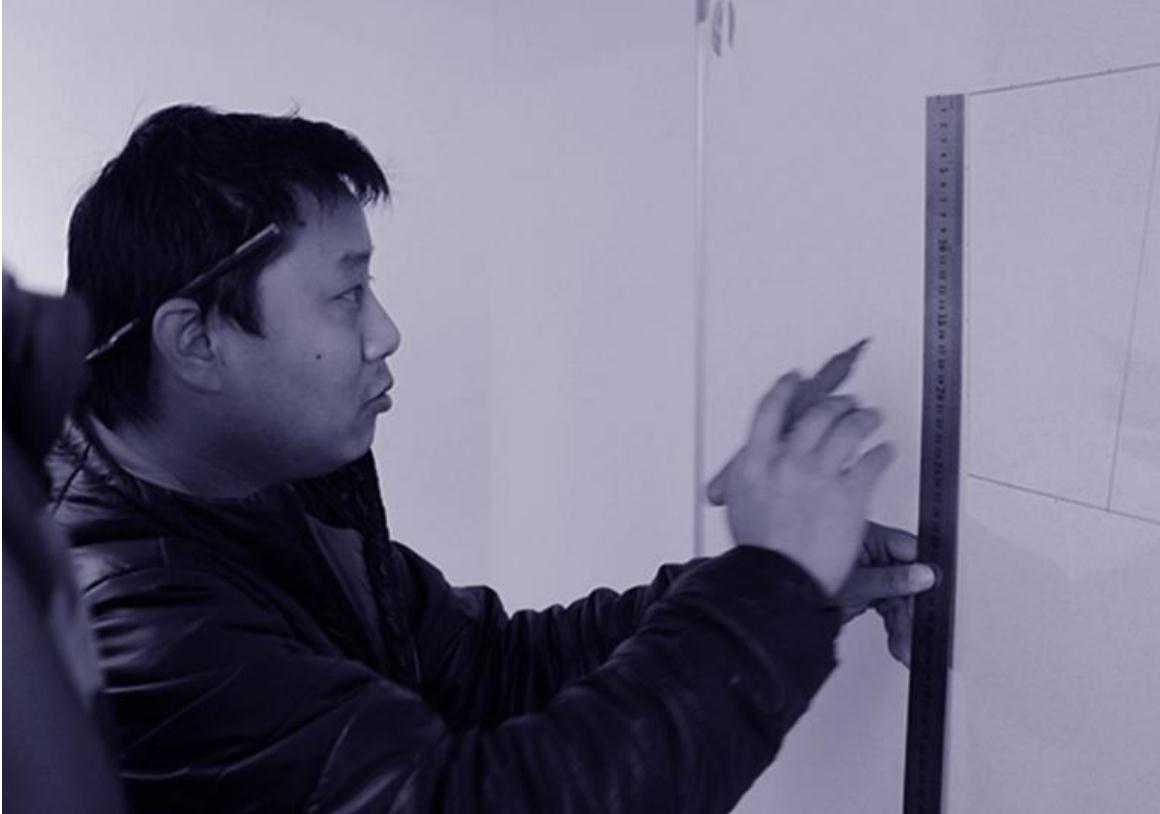
We start from timber sawing.
1. The timber veneer moisture balance
The timer veneers we use are through 2 times air dry and 1time kiln dry. Then the veneer will get to 6-10% moisture content. After we get the KD veneers, we will do the sanding/size reform, then we will use the plastic film to warp those veneers for stocking.
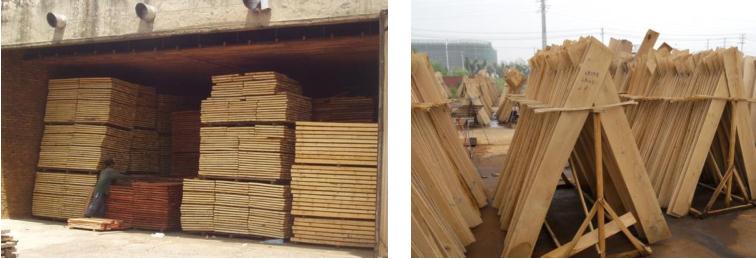
2. The plywood moisture control
The plywood are made by thin rotary veneers (1mm-2mm) which need to be dried in 4 steps: Log air dry/Oven dry/Hot press/Moisture Balance kiln facility.
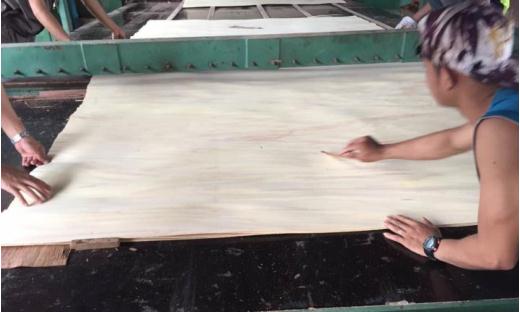
3. Veneer Sorting
Sorting out veneers based on grading standards required by orders accordingly.
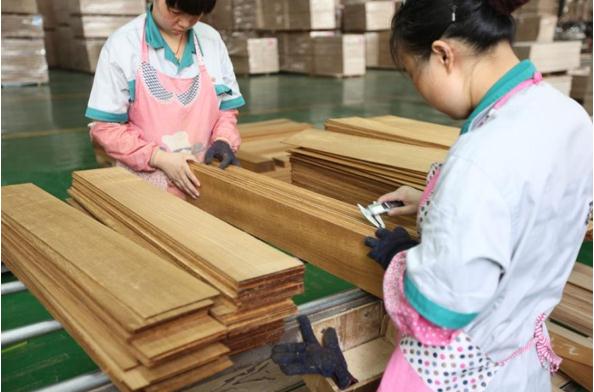
4. Balance Veneers and Plywood
Place veneers and plywood into the kiln for moisture balancing.
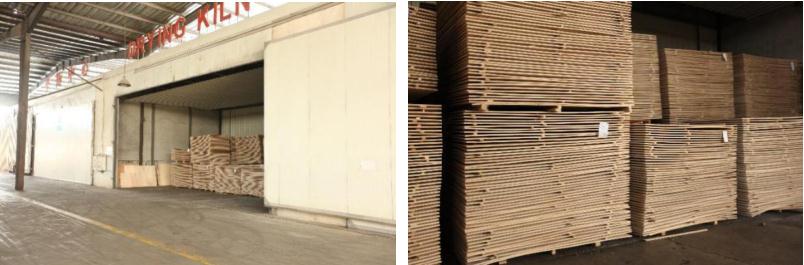
5. Veneer Cutting
According to designed pattern,laze cut the veneers if the veneer less than 3mm thickness, or by other saw machine.

6. Defects Repair
Fix knots and cracks with color-stained Epoxy resin.
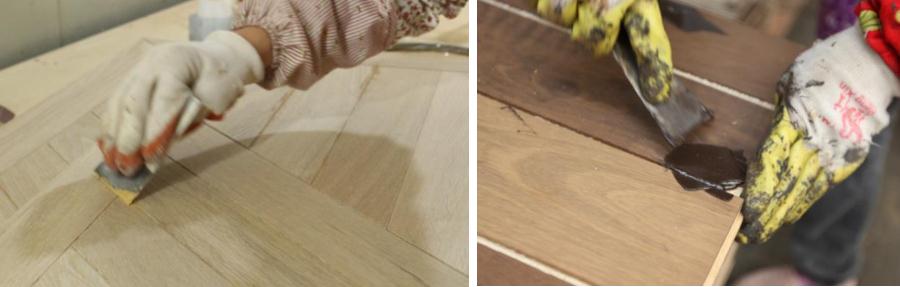
7. Cold Press
Cold press the balanced planks under the pressure of 800tons for 40 minutes.
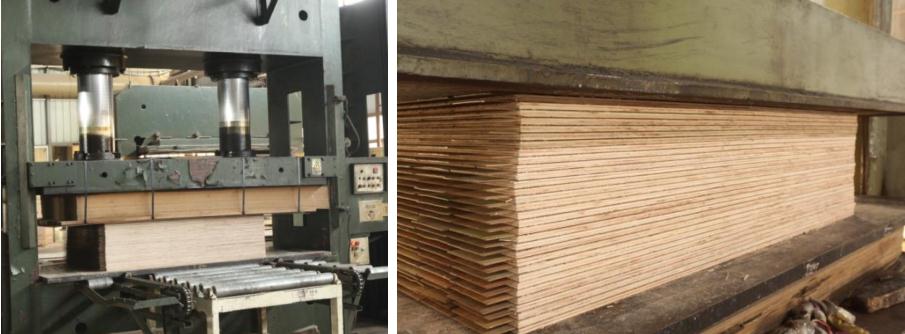
8. Accumulitization
Wrap the planks with plastic wraps and place in natural environment for 2 days accumulitization.

9. Pattern Piece Cutting
Cut the planks into pieces according to design patterns.
10. Sanding
Sand the surface of floor to get even thickness before final step production.
11. T&G and Bevel
We have to plan the Tongue or Groove for each side in each single shape to ensure that they can combine to the parquet.
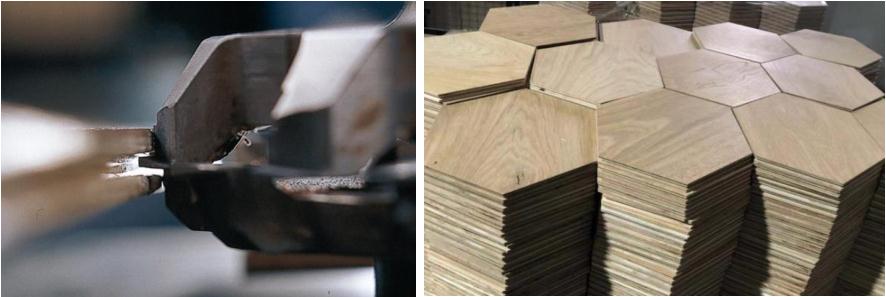
12. Surface Treatment
Like brush, handscraped, smoked, carbonized etc.
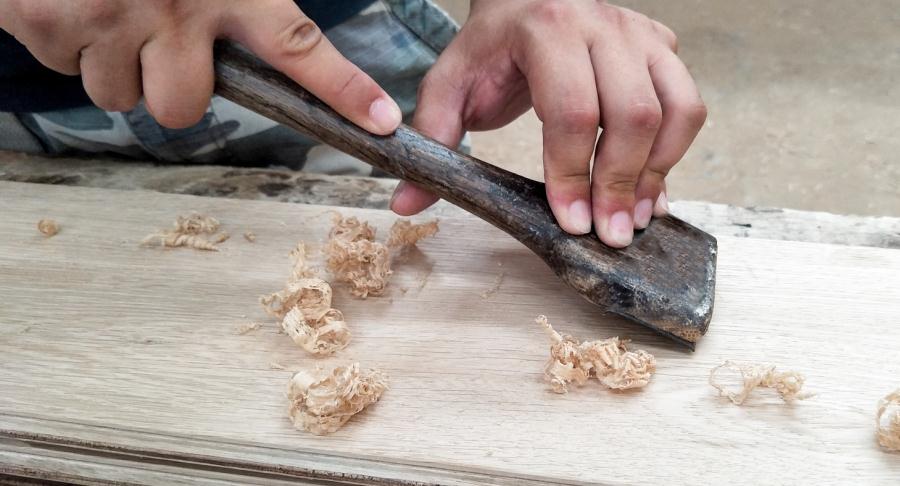
13. UV Lacquer or Oil Coating Finished
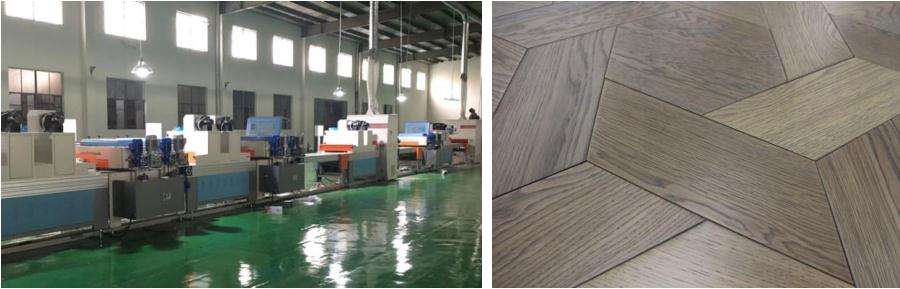
14. Packing and Loading
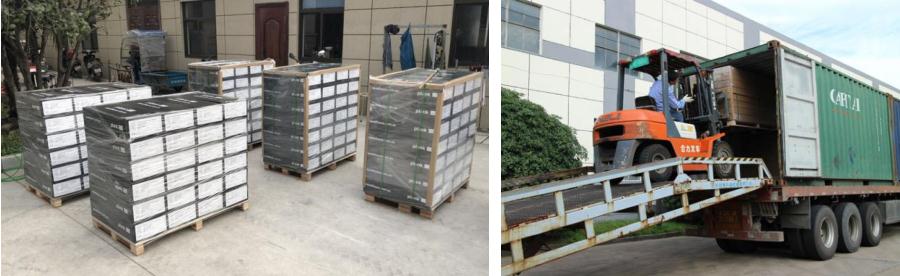