Strict Quality Control System
At LORD PARQUET, we are dedicated to offering the finest wood flooring solutions to our valued customers. Our commitment is rooted in providing top-quality flooring products to the global market, ensuring that every piece we deliver meets the highest standards of originality and craftsmanship.
Our Vision and Expertise
Founded on the principle of delivering superior flooring products, we specialize in designing colors and styles that align with worldwide indoor design trends. Our floors are crafted to enhance any interior space, reflecting the latest in global design aesthetics.
Global Presence and Seamless Service
With six strategic departments across the globe, LORD PARQUET ensures efficiency and excellence from production to installation:
- Headquarters: Hong Kong
- Sales & Shipping Supervision: Shanghai
- Quality Control Team: Zhejiang, China & Sihanoukville, Cambodia
- Customer Service: Sydney, Australia
- Oak Veneer Grading Team: Dalian, China
Our global team works in harmony to streamline processes and guarantee superior quality and service at every step. Whether you’re seeking advice on design, need assistance with shipping, or require quality assurance, LORD PARQUET is here to support you.
Under the control of ISO9001, ISO14001 and ISO14025, from material to the final product, each piece is processed through 49 working procedures and each procedure is controlled strictly by certain producing data. Especially for the procedures of kiln dry skills, environmental climates and piece checking, which promise our floor with a stable and high quality.
Sanding check before UV coating. Check the surface and thickness.
UV product line check, put away the defect UV coating product.
Final product color classified secondly. Make the final packed products color in most uniform .
Advanced kiln dry skills-key factor of final floor with a stable condition.
Drying the AD board according to the different species. Different species need different way (such as; time, temperature , Moisture etc.) to dry.
Before further processing, the dried boards just after taking out from the kiln need a stress-relief period. Different species need different stress-relief time. Then the AD board turned into KD board. The stress-relief period is very important for the stability of the floor.
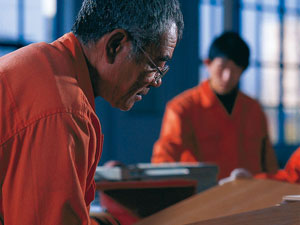
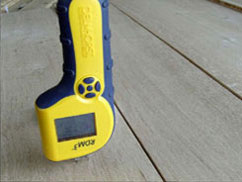
Moisture checking
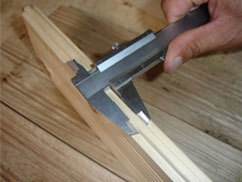
T&G profile checking
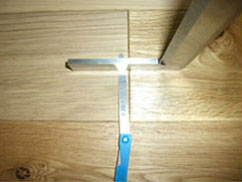
Glued Plywood
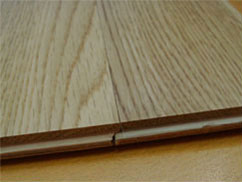
Square Edge
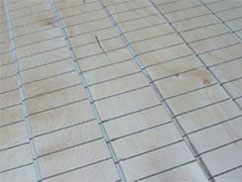
5.5mm Back Groove
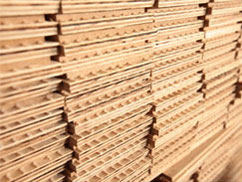
Moisture checking
Capacity & Location
We are equipped with:
- Germany Homag T&G Line
- Germany Weining T&G Line
- 8 Domestic Cold Press Machine
- One UV coating line (Taiwan Fengqiao)
- One Natural Oil line (Taiwan Fengqiao)
- Eight Kiln Dry Unit (80cbm each)
- 350 workers with 2 shift
- 80,000sqm Material Warehosue